A thousand lasers: why Opsys Point Cloud is a difference-maker in LiDAR accuracy
- Opsys Tech
- May 4, 2023
- 3 min read
Updated: Feb 13, 2024
How does Opsys Pure Solid-State Scanning LiDAR out-perform every other solid-state LiDAR available today? It’s all about the most advanced laser chip with a 2-D matrix of thousands of tiny laser emitters driven by Opsys’ proprietary driver chip, and the state-of-the-art single-chip 2-D receiver. Innovative engineering enables each of these tiny laser beams to reach 300 meters and scan the whole field of view (FOV) at an astonishing 1000 frames per second. This high frame rate increases the signal-to-noise ratio (SNR) by rejecting noise from solar radiation, reflections, and interference from external laser sources. The laser reflections from objects in the FOV are captured by the receiver in a 2-D array of data (the ‘image’) called the LiDAR point cloud.
So, what is a point cloud, and why does it matter in LiDAR accuracy? Here’s how it works.
A point cloud is the output of a LiDAR sensor. The transmitter bounces a laser beam off surrounding objects. Each laser is matched with a receiver, which catches the light that bounces back. The receiver knows how far away an object is by how quickly the laser light is returned from its paired transmitter. This is done over and over in rapid succession, covering all the objects in its field of view. The data locates each reflected point in space (in the x, y and z axes) and provides a measure of how reflective the objects are. Some LiDARs modalities can also provide the velocity of each point in the cloud.
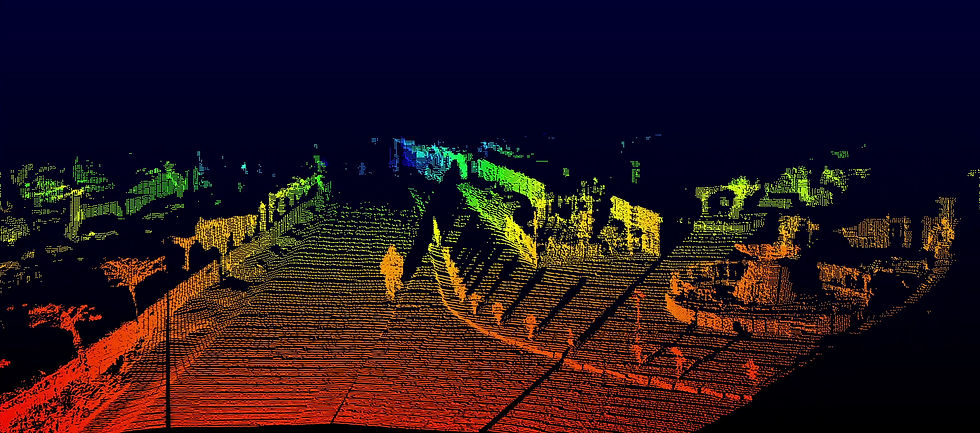
In LiDAR demonstrations, the visual representations of these point clouds look like granular images of cars, trees, or pedestrians. It’s important to keep in mind that these screens images are only part of what the vehicle processes. Of all the sensors that automakers use in their sensor fusion systems, LiDARs inherently provide the most exact digital representation of the environment around the moving vehicle for advanced-safety or automated driving systems. The car’s processor uses the LiDAR point cloud coordinates to create a three-dimensional view of its surroundings to inherently know the precise distances to objects in their surroundings and react appropriately. That 3-D image is what sets LiDAR apart from other sensors and that’s why it’s the gold standard for the data needed to make life-saving safety systems effective.
Other than range, LiDAR point cloud performance is characterized by the density of points (the resolution), accuracy of range measurements, the ability to detect objects with high probability, low false positive rates, and stability of points in the FOV. Sensors with a denser point cloud can put a greater number of points in an area, enabling the detection of smaller objects in the FOV. The rest of the parameters are necessary to ensure higher confidence in the point cloud data.
These are the parameters where the Opsys LiDAR sensor’s point cloud excels and is unmatched by any other solid-state LiDAR available today. Thanks to our electronic scanning technique, the Opsys LiDAR oversamples the full FOV at 1,000 frames per second. The sensor then averages the data collected down to 10 to 30 frames per second (as needed by the customer system). This means that every point of every frame in the point cloud is a result of multiple measurements. Spurious errors are eliminated to provide a much higher signal-to-noise ratio than possible with other solid state LiDAR architectures. With the ability to see objects as far as 300 meters away, and the ability to detect lower-reflectivity objects at longer distances, the Opsys LiDAR system creates a more detailed view with a higher probability of detection of objects.

All of this, in a small form factor sensor with no moving parts making it reliable, low power and low cost. The Opsys LiDAR sensor is scalable to different fields of view and provides different resolutions and max ranges to fit the required use cases to allow customers to design the best performance at the lowest cost. The Opsys LiDAR is truly the most advanced solid-state LiDAR available today.